Free knowledge to monitor the world of events. Have a look at our must read Blogs on Pharma, Finance, HR, Health and Cross Industry.
The Power of Root Cause Analysis
2022-08-16
Uncovering the Hidden Truth
In our previous blogs, we discussed on the psychometric tools that were used for recruitment. Imagine that when something goes wrong in a manufacturing facility, it’s not only important to address the issue but prevent it from happening again. Only by understanding the root cause of the issue can you stop it from recurring. So today we will be exploring the Root Cause Analysis in Informing CAPA.
To ensure the availability of goods and services that are of the highest quality, managing quality and continual development are essential in every industry. When an issue or deviation creates, it is of the utmost importance to identify its root causes and take appropriate measures to stop it from happening again. Root Cause Analysis (RCA) is then used in this scenario. RCA is a systematic approach that helps organizations in identifying the root causes of issues so that they can implement effective Corrective and Preventive Actions (CAPA). We will discuss the concept of root cause analysis and how it affects CAPA in this blog article.
Understanding Root Cause Analysis
An organized procedure called root cause analysis is used to determine the root cause or causes of a negative occurrence or problem. The objective is to investigate deeper than the symptoms that are apparent to identify the underlying causes of a problem. Organizations can prevent similar issues from occurring in the future by resolving their primary causes, which will enhance quality, efficiency, and customer satisfaction.
The Steps of Root Cause Analysis
1. Define the problem: Clarifying the problem or deviation that needs to be investigated is the initial step in RCA. Identification of the symptoms, the impact on stakeholders, and the specific issue that has to be solved constitute every part of this procedure.
2. Gather data: After the issue has been identified, it is critical to compile relevant information and facts about it. To develop a thorough grasp of the issue, this may involve examining documents, performing interviews, or analyzing the data at hand.
3. Identify potential causes: Potential causes are listed and discussed in this stage. It's crucial to consider all potential outcomes, whether they relate to the process, people, equipment, or outside forces. Finding potential causes can benefit from the use of brainstorming techniques like the "5 Whys" or fishbone diagrams (Ishikawa diagrams).
4. Analyze causes: The next step is to evaluate each potential cause to figure out its significance and impact on the issue. The causes can be prioritized according to their significance and probability using methods like Pareto analysis, statistical analysis, or Failure Mode and Effects Analysis (FMEA).
5. Determine the root cause(s): The root cause(s) are found from the list of possible causes. Effectively resolving the root cause will eliminate or significantly reduce the likelihood that the issue will return.
6. Develop CAPA: Corrective and Preventive Actions (CAPA) can be established once the root cause has been determined. While preventive measures are intended to stop similar problems from happening in the future, corrective measures seek to promptly address the existing issue. These measures could include process modifications, educational initiatives, policy adjustments, or equipment modifications.
The connection Between Root Cause Analysis and CAPA
For the development of an efficient CAPA, root cause analysis is vital. Organizations may discover a lot about the fundamental factors that lead to a problem by identifying its root cause(s). With this knowledge, they can create targeted CAPA that focuses on the recently identified causes, lowering the possibility of repetition.
Conclusion
Root cause analysis is an effective way of getting to the bottom of issues and identifying solutions. Organizations can avoid issues from recurring and constantly improve their processes, products, and offerings by identifying and fixing the issue's root cause(s). To enhance quality, consumer satisfaction, and overall organizational performance, effective Corrective and Preventive Actions (CAPA) are developed using the insights gleaned by RCA. Adopting a culture of RCA and CAPA allows firms to control risks effectively and encourage continuous improvement, which is an important investment in long-term success.
Are you ready to harness the power of CAPA and root cause analysis? Join our upcoming Masterclass on CAPA and Root Cause Analysis MasterClass conducted by industry expert.
By Nafhan Naseem, Jr. Social Media Executive & IT Support, GLC Europe, Colombo Office, Sri Lanka.
Get a feel for our events
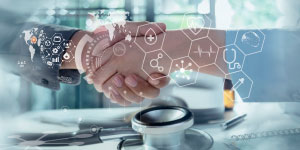
Sponsor Responsibilities in Clinical Trials MasterClass - US edition
02-03 September, 2025
Inspection readiness
learn more >>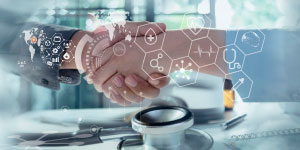
Sponsor Responsibilities in Clinical Trials MasterClass - EU edition
02-03 September, 2025
Establishing, Maintaining and Demonstrating Sponsor Oversight
learn more >>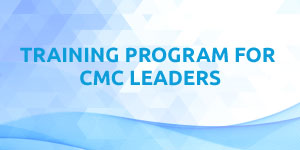
Training Program for CMC Leaders - EU edition
29th September 2025 - 24th April 2026
Rich with practical insights and real-world applications
learn more >>